Managing your heavy machinery safety and operating heavy machinery can both cause issues if the right systems aren't in place. In August 2014 a scissor lift accident killed a Lyttleton Port worker. The inquiry, a year later, found that the accident could have been avoided if an effective safety management system had been in place at the Port. The system could have identified key risk areas and ensured those risks were controlled.
The investigation identified several areas where not enough thought had been given to the risks posed to the Port workers. These key areas are important to any business that operates heavy machinery. They are:
- Maintenance
- Risk identification for each piece of machinery
- General operational checks including pre-start checks
- Operator and maintenance staff training
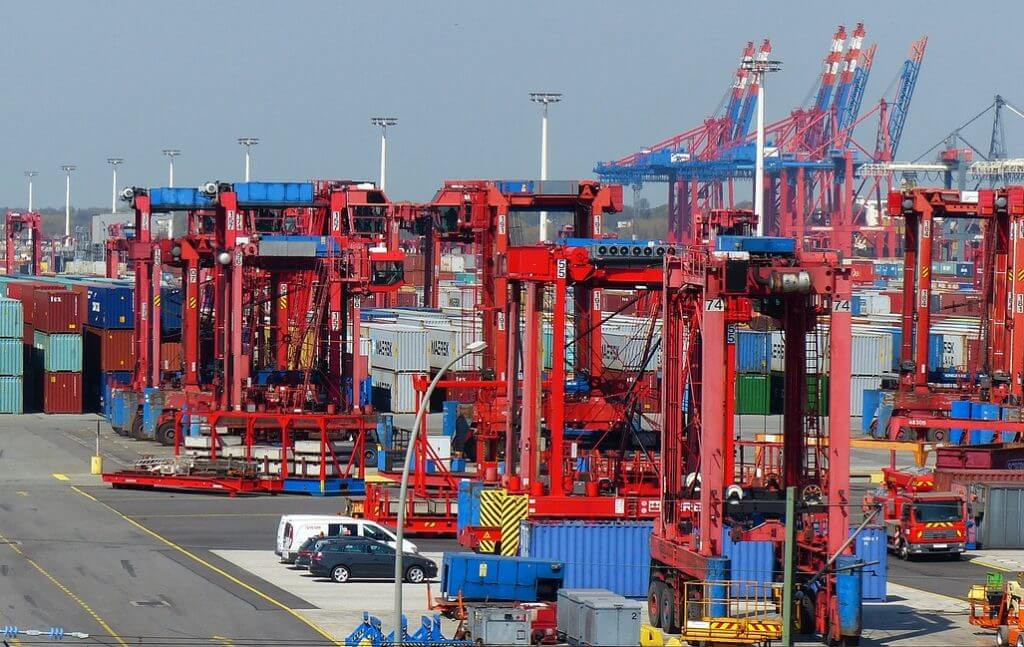
Heavy machinery can pose a risk to workers
Machinery needs regular maintenance. Different levels of machine servicing or maintenance should be scheduled. A simple clean down may be required at the end of everyday but a full engine overhaul only once a year. These maintenance records should be readily available to the machine operators, not filed away in the maintenance office.
A risk identification process is needed to identify potential hazards from the machines components or operating environment. In the case of the Port incident the out-rigger legs were found to be clogged with coal dust. Operating the machinery in an area with coal dust should have been identified as a potential risk to the equipment and steps taken to minimise the effects.
Pre-start checklists are essential when using machinery. A simple list with diagrams will help identify any potential hazards or faults. Faults can be recorded so that maintenance personnel can be notified if necessary or the machinery removed from use until repairs have been made. The operator should be able to see the service history and previous checks done on the machinery prior to its operation.
If operated incorrectly, machinery can be a danger to both the operator and workers nearby. It is very important that only people trained to use a specific piece of machinery operate it. Training registers should be kept to ensure operators have a current licence. Some machinery will also need specialist mechanics to maintain and repair the machinery. This was an one of the problems identified at the Lyttleton Port. Staff had little or no training on the maintenance of the scissor lifts.
Employers need to have a good understanding of how to manage the use of machinery and have instant access to training registers and checklists for the machinery being operated. Failure to do so could result in injuries to staff, disruption to the business and financial penalties.
Schedule a demo with our team to discover how Site App Pro can limit the risk to your machinery operators and the overall business. Give management real time access to machinery checklists and training registers and allow your machinery operators to carry out their pre-start checklists and risk identification via a smartphone or tablet.